Before installation,
the ball valve must be maintained through grease injection. The internal leakage only occurs at the valve seat and the O-ring of the valve seat. Damage and deformation of the valve seat during assembly, foreign matter in the seal groove (the internal seal groove), and damage of the O-ring (the external seal groove) are the main causes of internal leakage of
the ball valve. It is a key operation to maintain a new valve through injecting the grease in its grease nipple to judge whether it has trouble. The grease injection can be visually checked. Only when grease is evenly extruded from the valve seat and coated on the surface of the ball can the lubrication be maximized.
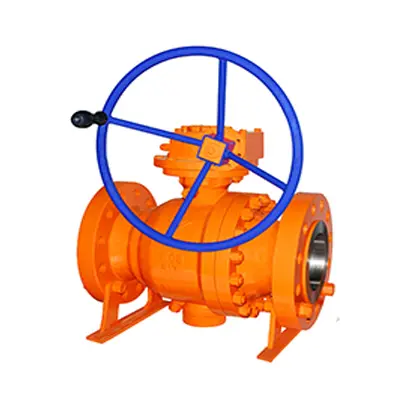
Through grease injection, not only can the sealing effect of the valve seat be visually seen, but also the quality of the O-ring can be checked. When it is found that the grease is extruded from the external seal groove or some black impurities flow out with the grease extruded from the valve cavity, it is necessary to check whether the O-ring is damaged.
Grease must be used instead of cleaning solution for grease injection of the valve, otherwise the O-ring will be softened, deformed and damaged. During the maintenance of internal leakage of the valve, the softening time of the sealing surface of
the ball valve soaked with cleaning solution should not exceed 12h, and then the valve should be opened and closed immediately to make the medium flowing in the pipeline wash away the cleaning solution. And grease should be injected again to reduce the influence of the cleaning solution left in the grease injection passageway on the O-ring.
In the process of valve installation, fine particles (e.g. dust in the construction site) will directly affect the operation of the valve. The grease on the internal seal groove can effectively block the embedding of small particles in the valve.