The failures of the valve mainly include failures caused by fractures, failures caused by corrosion, failures caused by leakages and failures caused by wear. The part with the most failure caused by fractures and corrosion is the valve stem, and the part with the most failure caused by leakages and wear is the sealing part. The characteristics of failures caused by fractures, corrosion and wear can also be further distinguished from the characteristics of the fracture path, fracture speed, color and composition of corrosion products, size of grooves and abrasive particles. In addition, more specific classification and identification methods are studied for failures caused by leakages.
Failures of valves are often the result of a combination of factors. The improvement in failures of valves can be started from the two aspects, such as structure and processing technology.
Improvement in structure
The improvement in the structural aspect is mainly to avoid stress concentration, optimize the sealing structure and change the flow characteristics, and effectively avoid failures caused by fractures, leakages and wear. Table 1 lists the structural improvement from domestic and foreign scholars for the problem of stress concentration. Structural improvement is conducted to avoid stress concentration and effectively avoid failures caused by fractures.
Table 1 Structural improvement cases with stress concentration
Researchers |
Types of failures |
Parts |
Measures |
Sotoodeh |
Failures caused by brittle fractures |
Ball valve stems |
Change the calculation method of the stem’s diameter to increase the maximum allowable torque. |
Zhi Zhang |
Failures caused by fatigue fracture |
Plug valves |
Chamfering or setting stress relief grooves should be adopted. |
Fengmin Yang |
Failures caused by fatigue fracture |
Hot blast valve plates |
The stress concentration part is far away from the heat affected zone of the welding seam. |
Yufeng Wang |
Failures caused by plastic fractures |
Gate valve seats |
Increase the size of the valve seat to enhance the overall stiffness. |
Optimizing the sealing structure is the most effective way to avoid failures caused by leakages. Xinlei Yao and others improved the structure of the rubber sealing ring, using a large arc sealing ring to replace the small arc sealing ring, and obtained better resistance to permanent deformation. Jie Liu and others improved the structure of the flange sealing part of the boundary valve, and the gasket surface was additionally pressurized by 10 MPa; the sealing effect was good after testing.
Changing the flow characteristics starts by changing the structure of the flow channel to control the flow direction and flow rate of the fluid inside the valve so as to avoid failures caused by leakages and wear. In view of failures caused by leakages, Ming Hu and others pointed out that the unreasonable design of the flow channel will cause the inlet gas to form a vortex on the sealing surface of the flange at the bottom of the valve seat, as shown in Figure 2, which will cause repeated scouring of the sealing surface and lead to leakages of gas. For the failure of corrosion and wear, Xiaodong Zhang and others pointed out that a reasonable selection of the incident angle of liquid flow can reduce the wear of the valve spool's sealing surface.
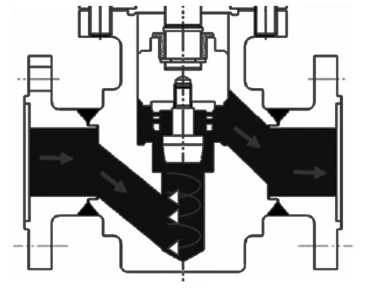
Figure 2 Flow channels with unreasonable structure
Avoiding stress concentration through structural optimization is an effective way to improve failures caused by fractures. Optimizing the sealing structure and controlling the initial sealing specific pressure is an effective way to improve the failures caused by leakages at present. The effect of improving the flow characteristics is very good, but the improvement is difficult. In the future, the influence of different valve flow channel structures on failures caused by leakages and wear should be analyzed. At present, the improvement method of failures caused by fractures is relatively simple, and the structure of components needs to be innovated in the future to obtain better force distribution. Quantitative analyses of the specific pressure of the seal and the formation of an empirical formula is an important research method to avoid partial failures caused by leakages in the future.
(2) Improvement in the processing technology
Table 2 lists the domestic and foreign scholars' research on the improvement in processing technology. Improvements in the processing technology are mainly to avoid failures caused by leakages and corrosion.
Table 2 Improvement cases of processing technology
Researchers |
Types of failures |
Objects required improvement |
Measures |
Minghui Ouyang |
Failures caused by galvanic corrosion |
Butterfly valves |
Improve casting process and heat treatment to increase the density of the coating. |
Daitao Gong |
Failures caused by crevice corrosion |
Butterfly valve discs |
Replace the material with nickel ductile iron with higher Ni content. |
LUO |
Failures caused by galvanic corrosion |
Nitriding processes |
Reduce nitriding time; lower temperatures and perform secondary oxidation treatment. |
Qimin Zhu |
Failures caused by the surfacing layer |
Surfacing processes |
Preheat before welding and perform slow cooling after welding. |
The measures to avoid failures caused by corrosion usually include using corrosion-resistant materials, coating treatment, and cathodic protection treatment. The use of corrosion-resistant materials is a direct means to solve corrosion, but some corrosion-resistant materials are expensive and cannot be widely used. The coating is currently the most widely used anti-corrosion measure in the valve industry. However, the porous coating is likely to form a corrosion channel with the coating surface of the valve parts and accelerate the galvanic corrosion. Therefore, it is necessary to ensure a dense coating. Similar to failures caused by corrosion, avoiding failures caused by leakages is also from the perspective of improving the quality of the surfacing layer. In the future, it is of certain significance to study how to improve the service life of parts after the coating fails, and to reduce the failure rate of the parts. Although some achievements have been made in the improvement of structure and processing technology, the economic cost of improvement measures is not considered. In the future, a comprehensive evaluation of performance and economy should be carried out on the cost of structure and processing technology.